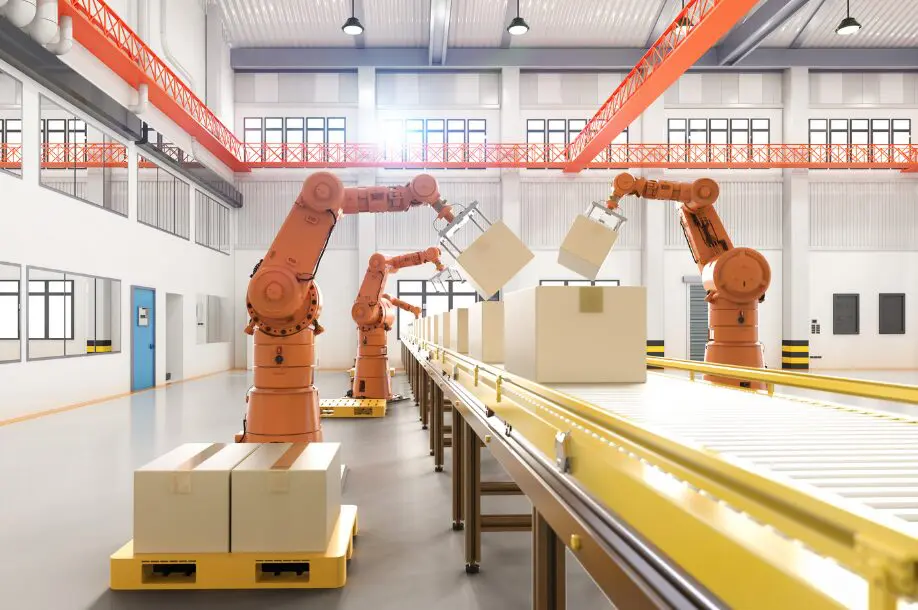
In an era where technology drives efficiency and data fuels decision-making, warehouse operations are evolving at breakneck speed. From autonomous mobile robots (AMRs) and artificial intelligence (AI) systems to warehouse management software and real-time tracking, warehouses have never been more advanced. But amidst this surge in innovation, it’s worth asking: are we going too far? Are we at risk of overcomplicating what should be streamlined and straightforward?
The Drive for Digital Efficiency
Modern warehousing technology offers undeniable benefits: reduced manual labour, increased picking accuracy, optimised storage, and faster order fulfilment. Automated systems can operate 24/7, AI can predict demand patterns, and Internet of Things (IoT) devices can monitor equipment health to pre-empt maintenance needs.
This tech-forward approach is largely a response to customer expectations. As e-commerce grows and delivery times shrink, warehouses must keep pace by working smarter and faster. Technology provides a pathway to do just that.
According to a 2024 Warehouse Technology Survey by Logistics Management, operations implementing advanced automation solutions reported an average 27% increase in productivity and 32% reduction in picking errors. For high-volume facilities processing thousands of orders daily, these improvements translate to significant cost savings and competitive advantage.
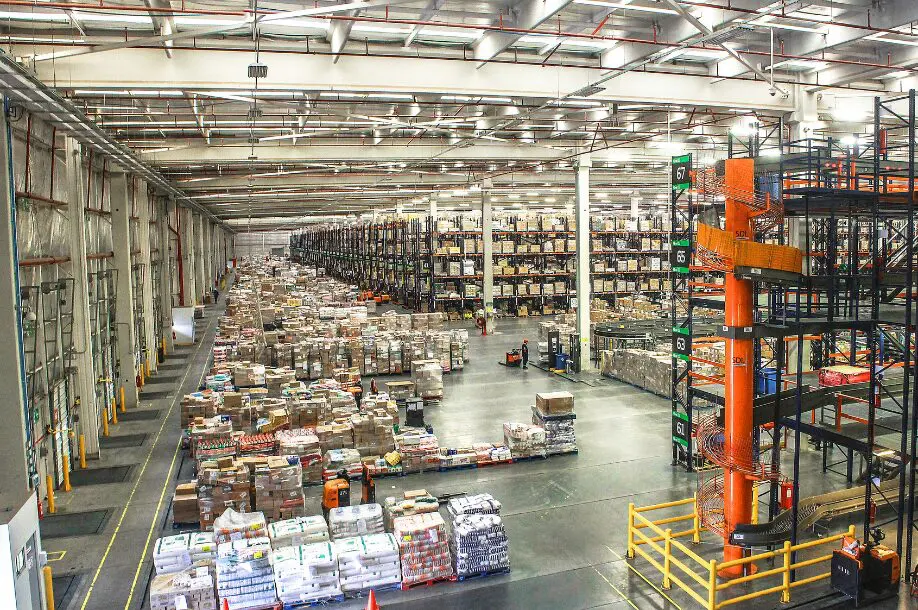
The Hidden Complexity
However, with every new layer of tech, the landscape becomes more complex. Systems need to be integrated, software requires updates, and staff must be trained (and retrained) regularly. When multiple platforms manage inventory, logistics, maintenance, and analytics, compatibility issues and inefficiencies can arise.
Moreover, the capital investment needed to adopt cutting-edge solutions can be significant. For smaller businesses or those operating in legacy facilities, this barrier can create a digital divide, where some operations surge ahead while others fall behind.
Case Study: The Cautionary Tale of MaxSpeed Fulfilment
In 2023, MaxSpeed Fulfilment invested £4.2 million in a comprehensive technology overhaul, implementing an advanced WMS, automated sortation system, and fleet of picking robots simultaneously. Six months later, they were dealing with system integration problems, staff frustration, and fulfilment rates worse than before the implementation. The company ultimately had to pause half of their new systems while they rebuilt processes from the ground up, costing them both time and customer confidence.
The Human Element

Technology can support the workforce, but it should not replace its value. Over-automation risks alienating experienced workers, reducing human oversight, and creating environments
that rely too heavily on systems. When something goes wrong, whether a software glitch or hardware malfunction, it often takes human insight to resolve it.
Striking the right balance between automation and human intuition is critical. Employees are often the first to spot bottlenecks, inefficiencies, or opportunities for improvement that algorithms might miss.
Research from the Institute of Warehouse Management found that operations maintaining a “technology-assisted human workforce” model experienced 18% fewer critical system failures than fully automated alternatives. They were also able to recover from disruptions an average of 40% faster, highlighting the resilience that comes with maintaining human oversight.
Technology Assessment Framework
Before implementing new warehouse technology, consider these critical questions:
- Problem Identification: What specific operational challenge are we addressing?
- Alternative Solutions: Could this be solved through process improvement or simpler means?
- Integration Capability: Will this technology work with our existing systems?
- Total Cost Analysis: Beyond purchase price, what are the implementation, training, and maintenance costs?
- ROI Timeline: How long until this technology pays for itself?
- Scalability: Can this solution grow or adapt as our business evolves?
- Human Impact: How will this affect our workforce, and what support will they need?
Warehouses should continuously evaluate whether their technology stack aligns with operational goals. Are the tools in use genuinely solving problems, or are they introducing new ones? Are systems scalable and adaptable as business needs change?
Industry-Specific Considerations
Different warehouse operations face unique technology considerations:
E-commerce Fulfilment
With high SKU counts and individual picking requirements, e-commerce warehouses often benefit most from pick-to-light systems and sortation automation. However, their seasonal demand fluctuations mean systems must be flexible enough to scale up and down rapidly.
Cold Storage
Temperature-controlled environments bring additional challenges for technology implementation. Batteries perform differently, and electronics may require special housing. Before investing in automation, cold storage operations should ensure solutions are specifically designed for their environment to avoid costly failures.
Manufacturing Support
Warehouses serving manufacturing operations typically benefit more from inventory accuracy technologies and just-in-time delivery systems than from picking speed enhancements. Their technology priorities should align with production needs rather than distribution metrics.

Manufacturing Support
Warehouses serving manufacturing operations typically benefit more from inventory accuracy technologies and just-in-time delivery systems than from picking speed enhancements. Their technology priorities should align with production needs rather than distribution metrics.
Success Through Strategic Implementation
Case Study: Phased Excellence at Regional Distribution
Regional Distribution Ltd took a different approach than MaxSpeed, implementing new warehouse technology in carefully planned phases over 18 months. They began with core WMS improvements, ensuring data integrity before adding automation. Staff were involved in each implementation decision, with dedicated “technology champions” trained ahead of each rollout.
The result: 35% productivity improvement, 44% error reduction, and perhaps most importantly, 92% staff satisfaction with the new systems. Their phased approach cost 15% more upfront but delivered ROI three months earlier than projected due to smoother transitions and fewer disruptions.

Conclusion: A Smarter Path Forward
Warehouse innovation isn’t inherently negative; in fact, it’s vital. But innovation for innovation’s sake can do more harm than good. The smartest operations are those that critically assess what tech to adopt, when to implement it, and how to support it with skilled people and processes.
The most successful warehouse operations follow these principles:
- Targeted Implementation: Focus on technologies that address specific operational challenges
- Phased Rollout: Implement changes in manageable segments with time for adaptation
- Workforce Involvement: Engage employees in technology decisions and implementation
- Continuous Evaluation: Regularly assess whether technologies are delivering expected returns
- Balanced Approach: Maintain appropriate human oversight of automated systems
Asking whether we’re adding too much technology isn’t a call to reject progress; it’s a reminder to keep it purposeful, manageable, and aligned with long-term strategy. Because in the end, the best warehouses aren’t just the most automated—they’re the most adaptable.