
Your paintshop is the last process in a long string of manufacturing processes, and it’s often one of the most overlooked as well.
There are several things you can do to significantly upgrade your painting process and save significant amounts of time and money, all while improving the painted finish and upgrading operator safety.
In this article we’ll cover:
- Testing paint colours
- Recording batch numbers
- Employee ergonomics and safety
- Making time for cleaning
- Workspace layout
- Overspray
- Upgraded spray guns
- High flow air fittings
- Spray booth coatings
- Lighting
- Solvent recyclers
- Automatic gun cleaners
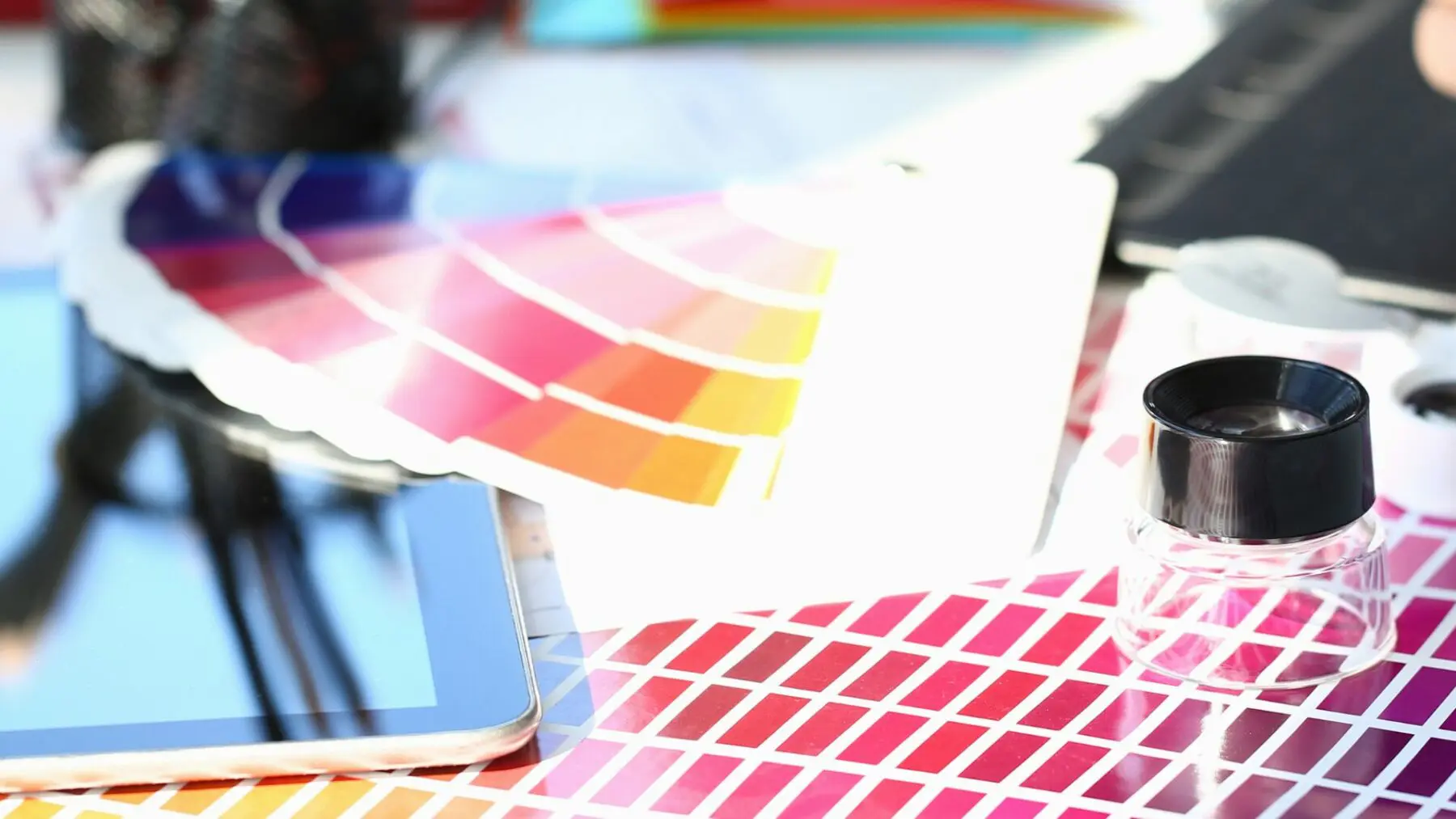
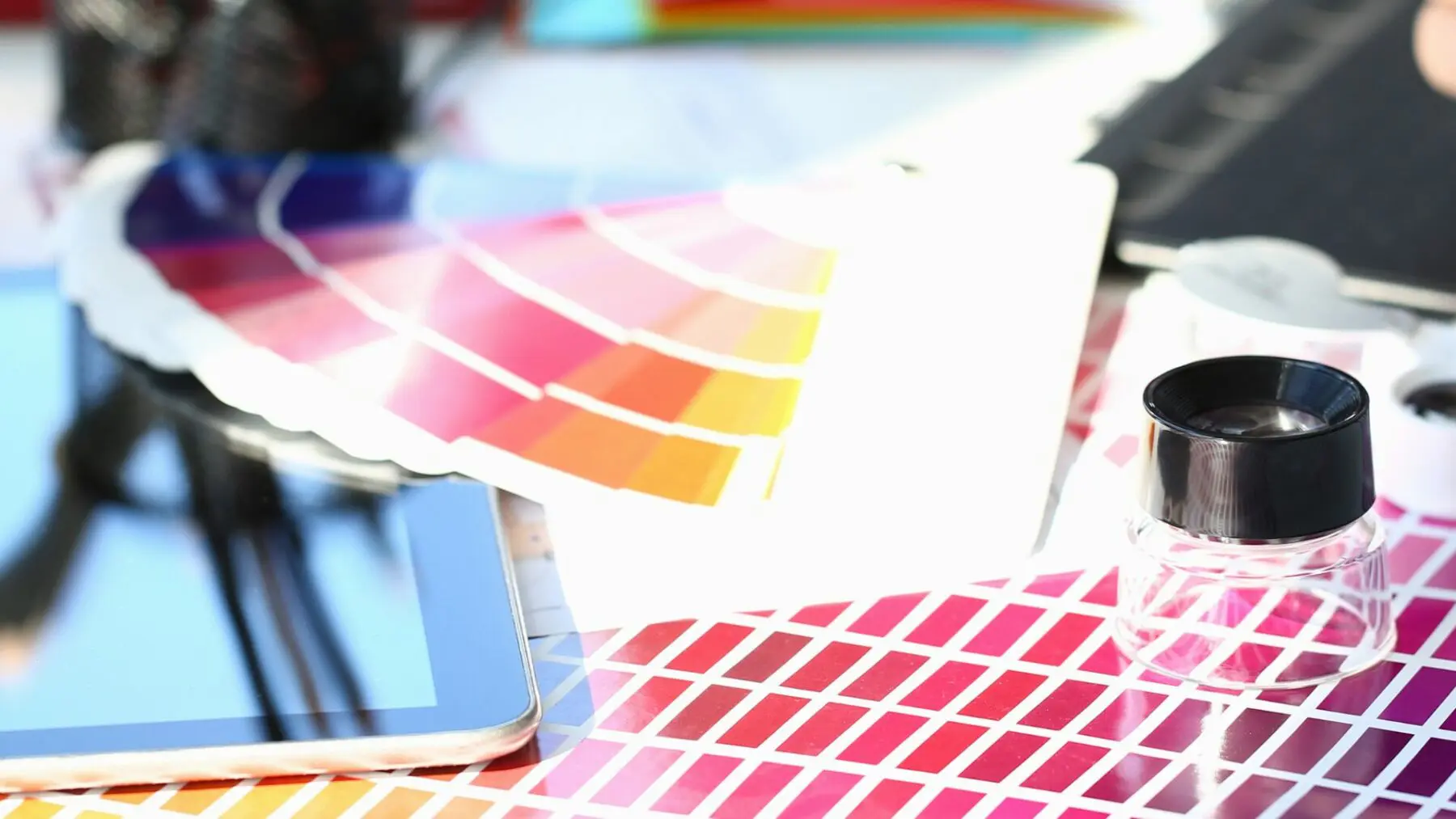
Test paint colours
Whether you get paint pre-mixed, free-issued or if you mix it in-house, it’s vital that you check the colour before starting the work. Approximately 5% of paint colours supplied pre-mixed are not accurate enough to be used, and depending on the finished article, this can cause huge amounts of rework and lost profit. Part of this is because when paints are mixed, they are a “close interpretation” of a colour standard like BS or RAL and there is a slight tolerance for variation.
In addition to this, metallic or pearlescent paint finishes can vary depending on the spray gun or application method.


Record batch numbers
Any reputable paint supplier will keep strict quality records and will have stringent quality control processes, so it’s important to record the batch number of every tin of paint, hardener, thinner or additive that you use on every paint job. This way, if there is an issue with the product, it can easily be traced back and measures taken to rectify the issue. If you’ve not kept records, there’s no way that faulty products can be identified accurately.
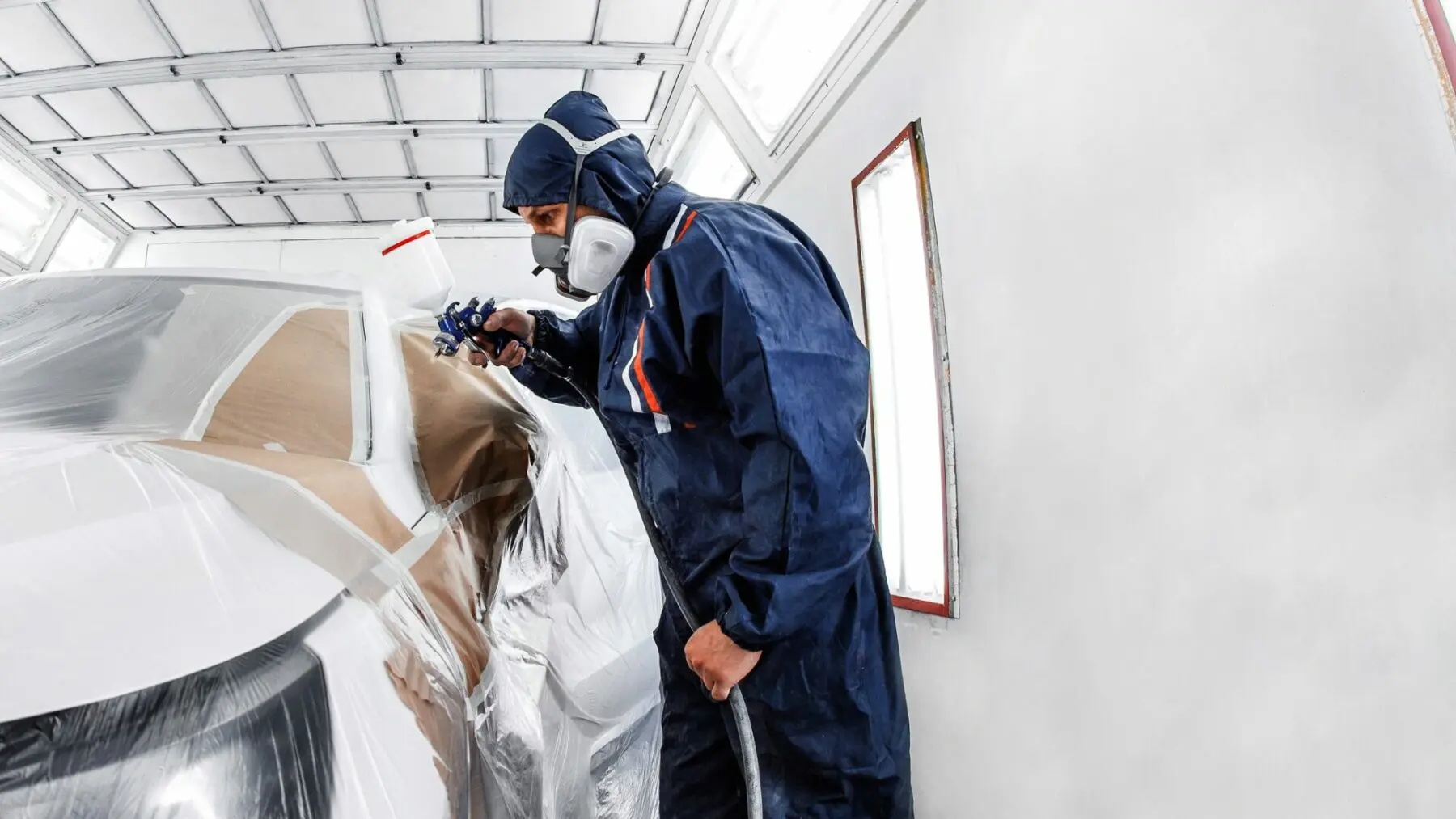
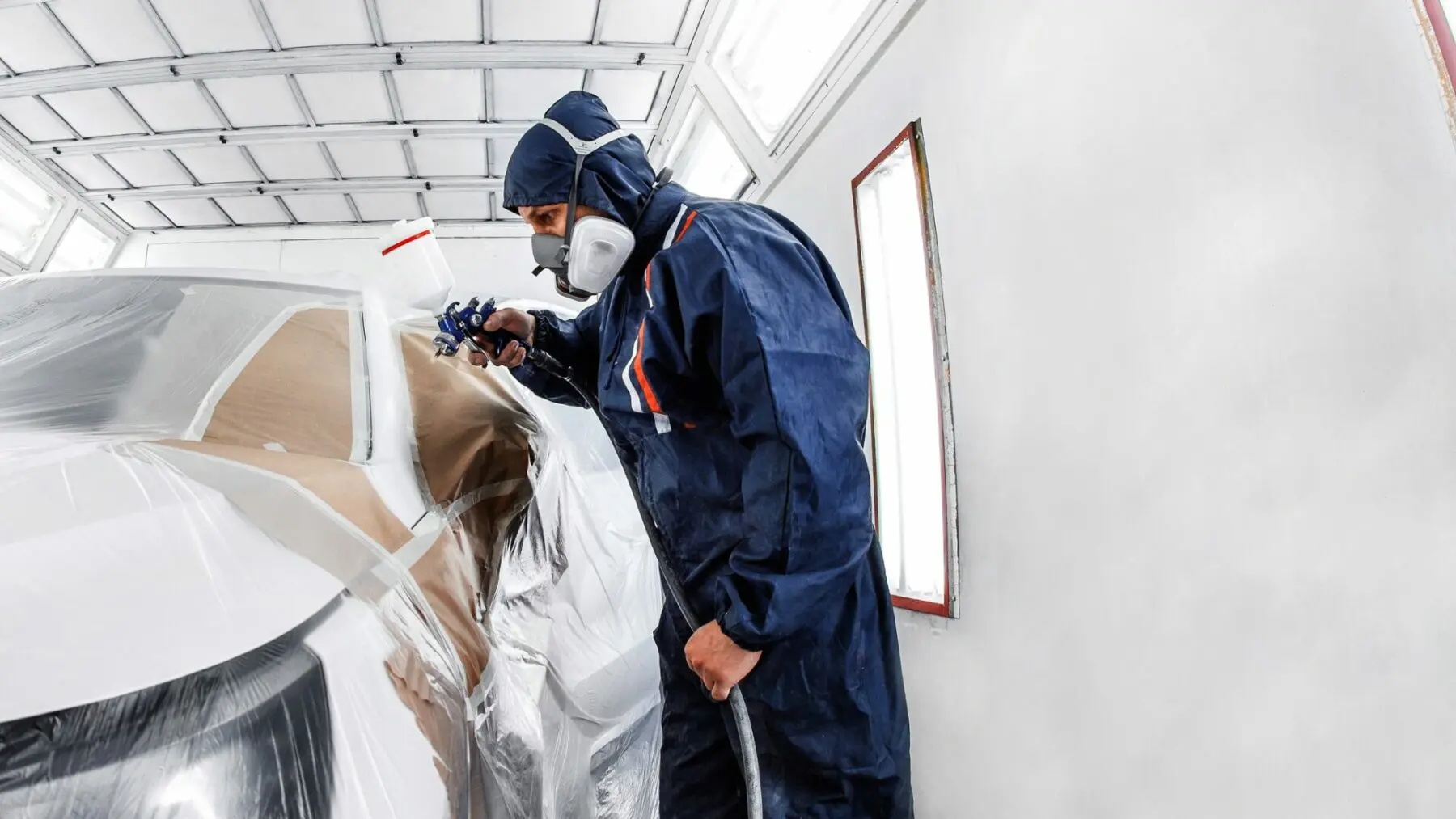
Operator ergonomics and safety
Often overlooked, there’s nothing more important than ensuring the safety of the employees in the spray booth. This isn’t only from an employer’s obligation for safety, but this is also important from a business continuation perspective as sprayers aren’t easily replaced in the short term! Ensure that your sprayers have all the correct equipment they need including the right gloves, coveralls, eye protection, anti-static footwear, and breathing equipment they need to do the job safely.
In addition to this, things like rotating spray tables, magnetic clamps, drying racks and even conveyor systems can make a substantial improvement to throughput and efficiency.
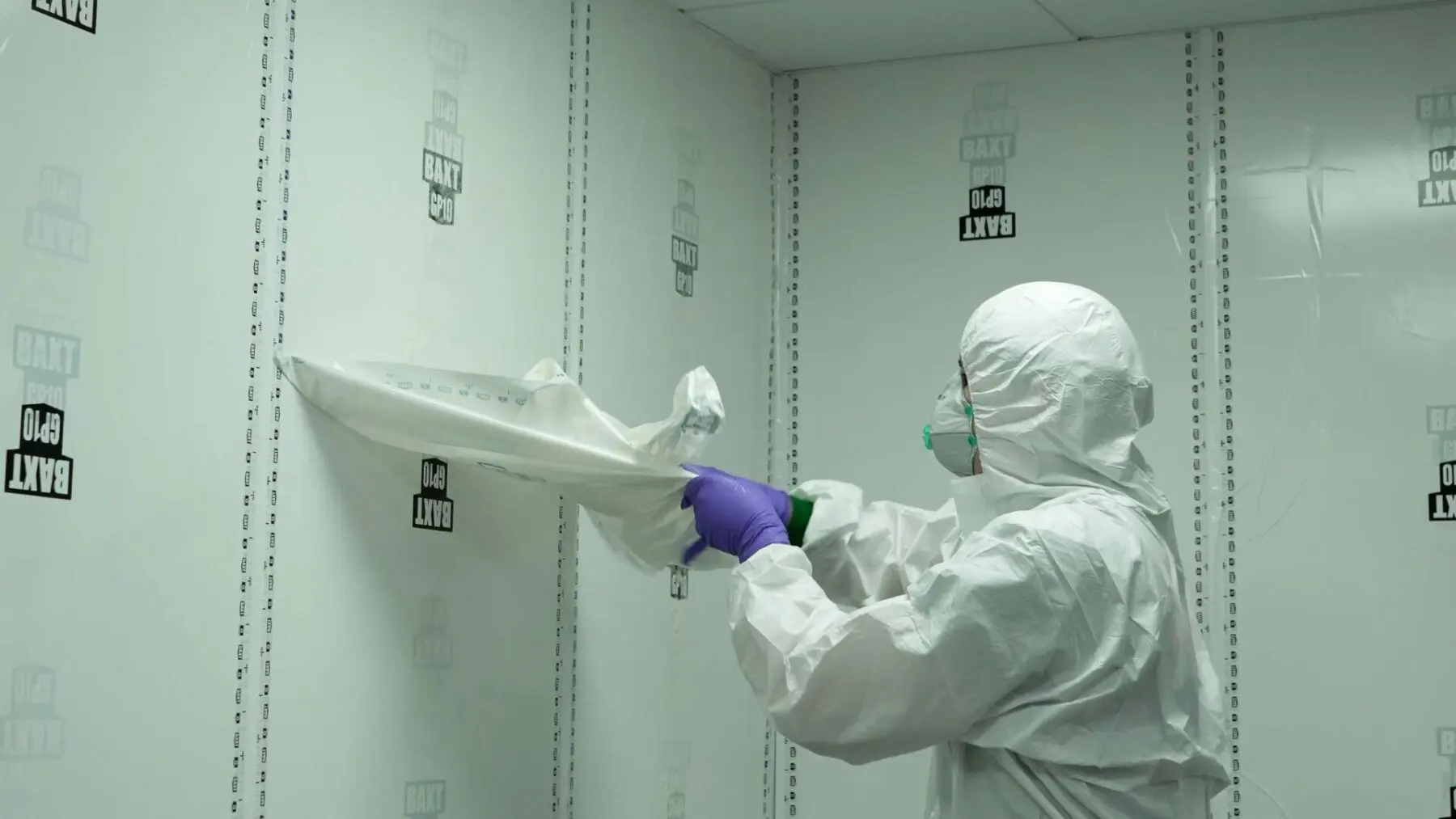
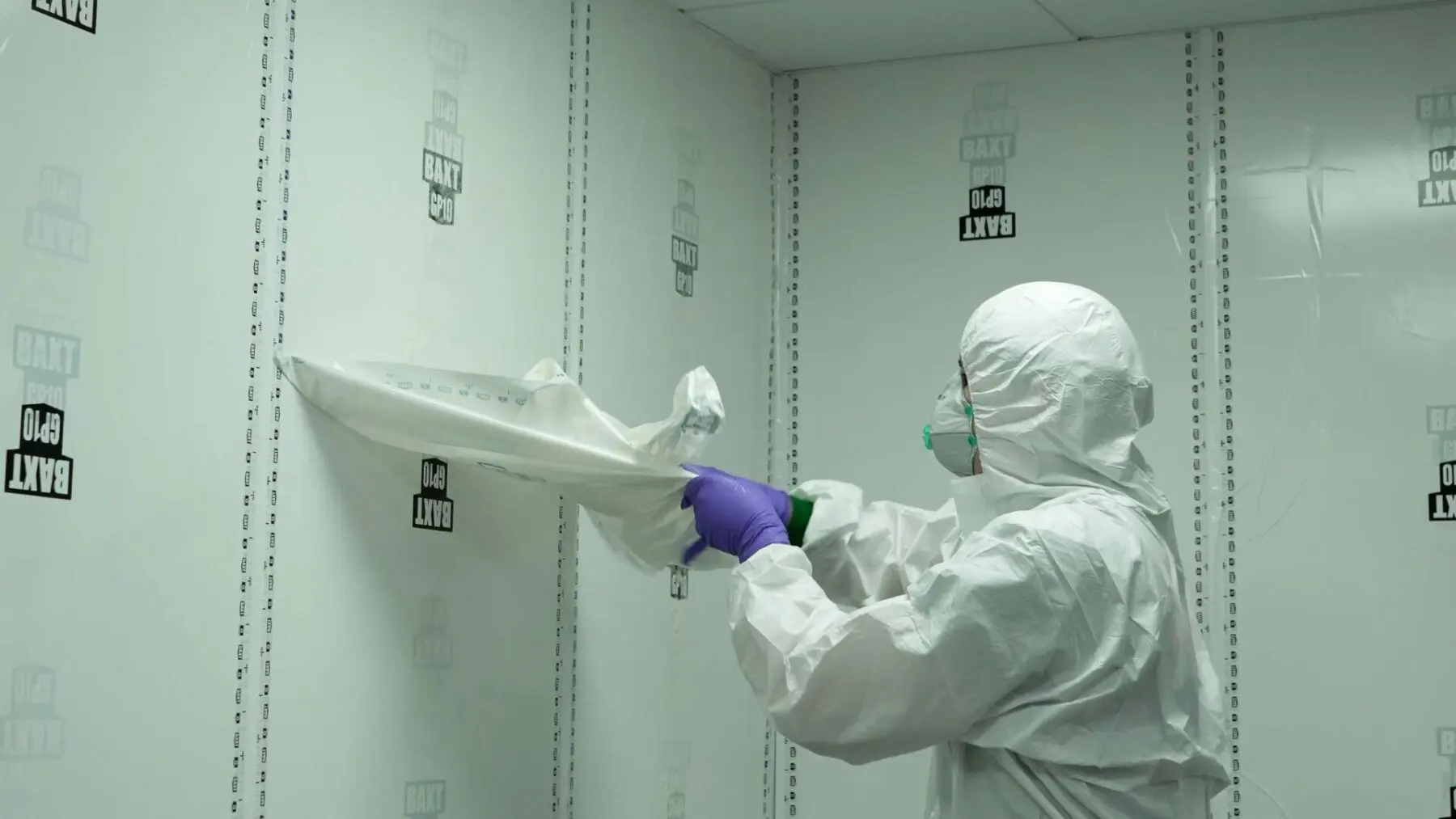
Make time for cleaning
Everyone likes a clean spraybooth, but not everyone always has one! It’s important to schedule time in your production calendar for daily, weekly, monthly, and annual cleaning and maintenance tasks. A clean and tidy spray booth will make a surprisingly significant difference to quality of work and employee morale.


Optimise workspace layout
Continuing from an earlier point about ergonomics, spend some time observing your paintshop process and analyse where there is wasted movement and time spent between tasks. Consult with your sprayers and discuss the principles of workflow efficiency and how to best apply them to your setup.
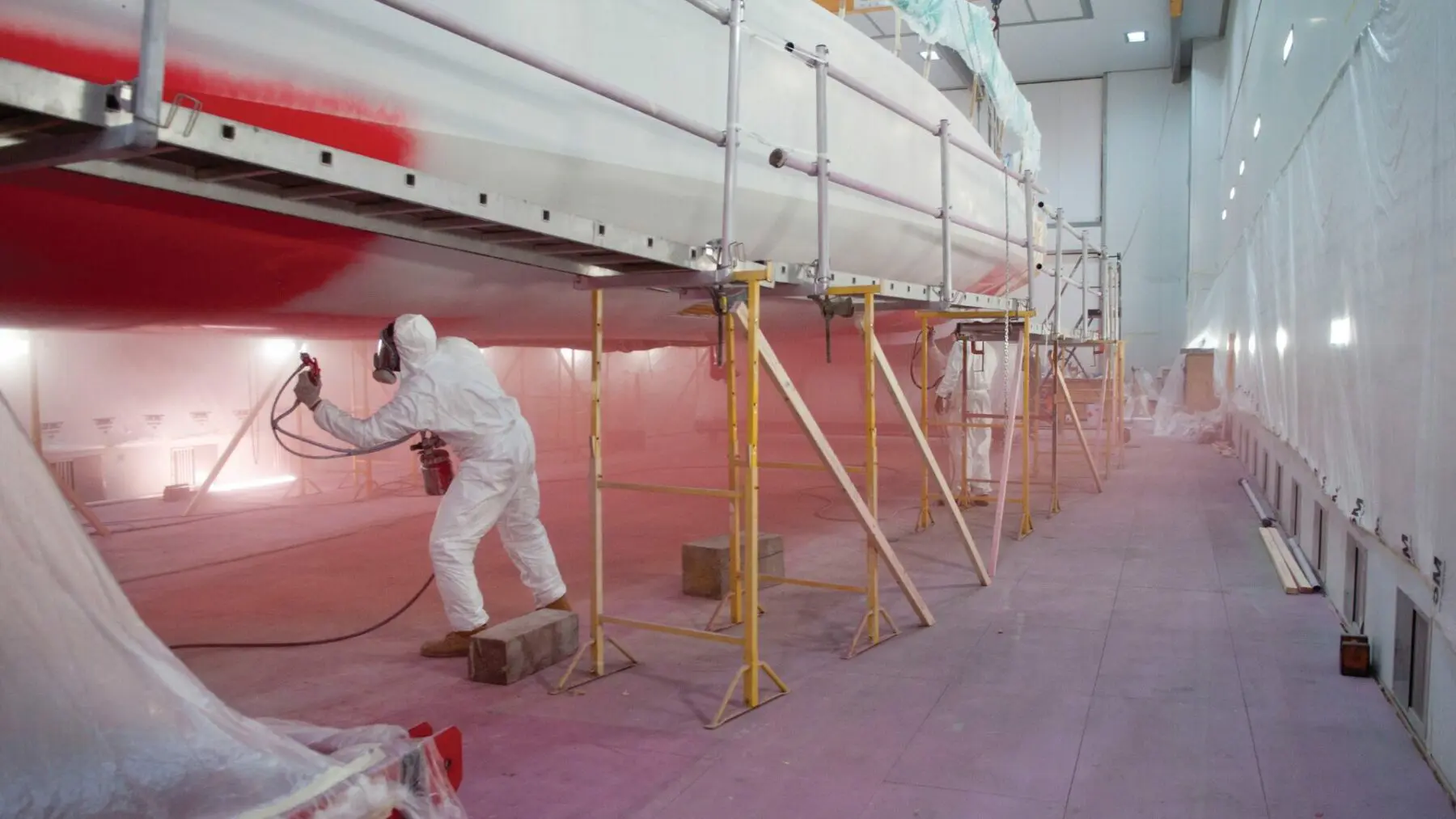
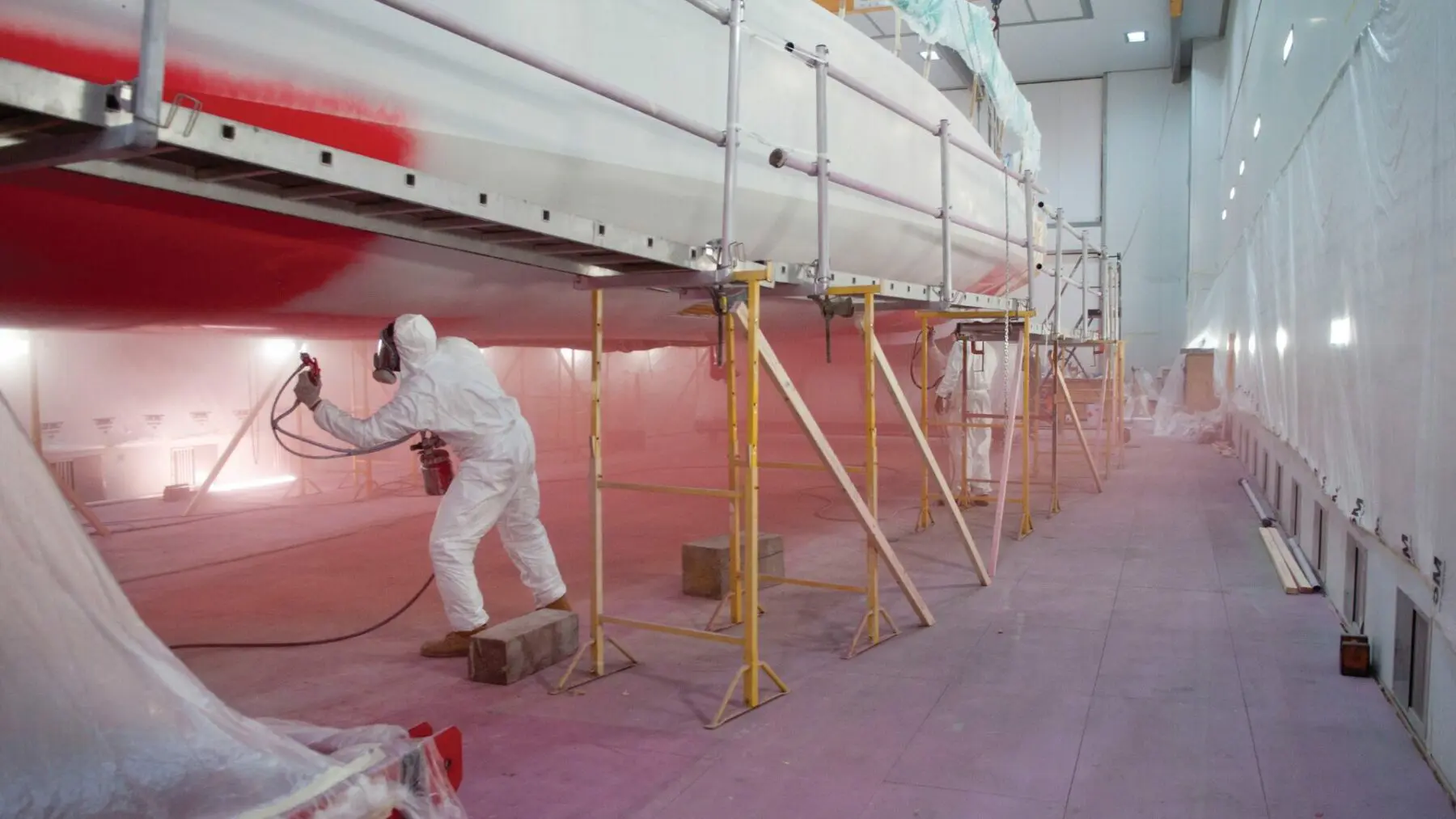
Fix overspray issues
Poor extraction will inevitably lead to overspray issues in the spraybooth which in turn leads to costly rework and a poor-quality finish.
By regularly changing the booth filters (or upgrading them altogether) you’ll significantly improve the quality of the air. A manometer is a small but useful investment you can make to check that you’re getting sufficient airflow.
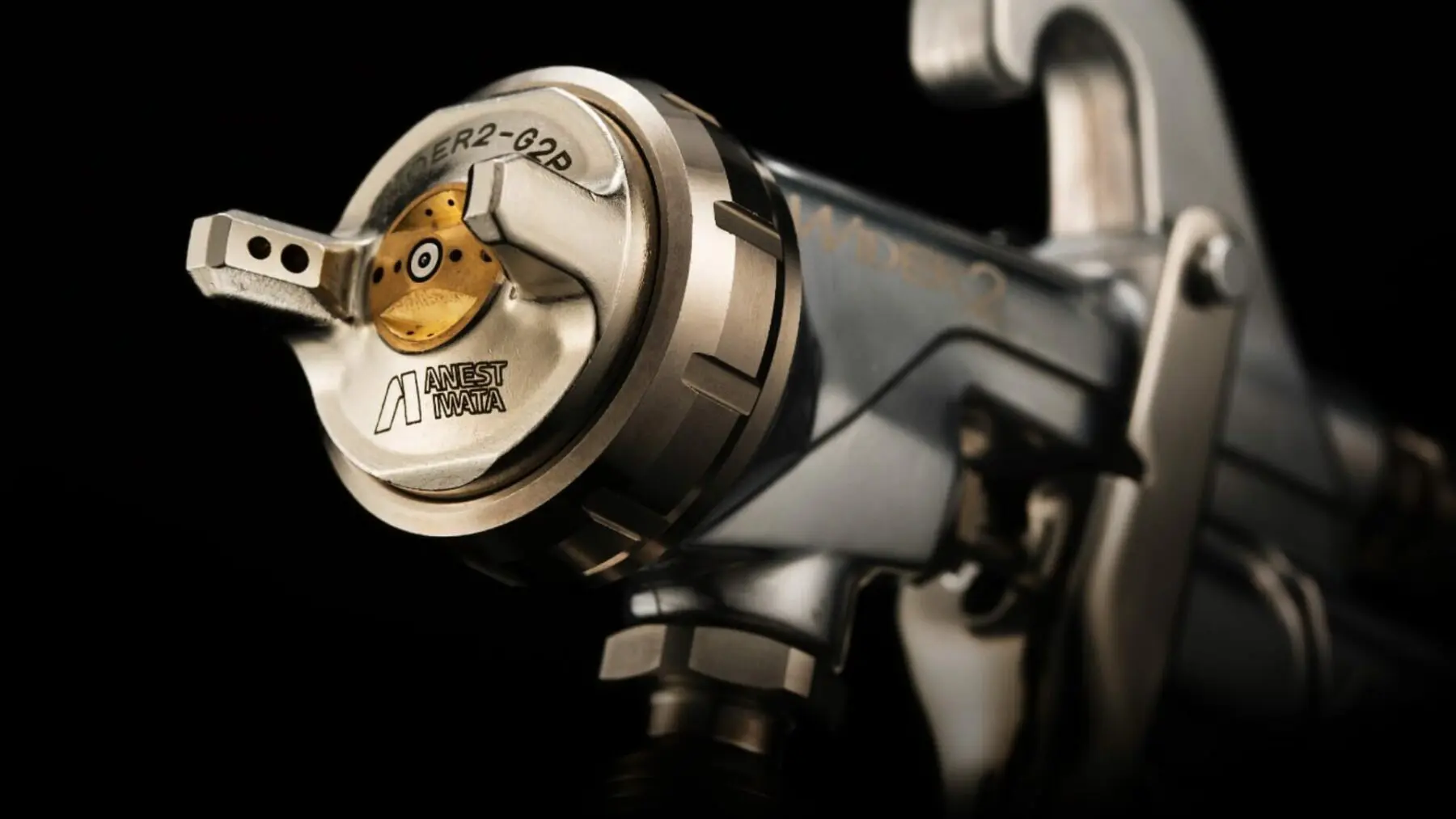
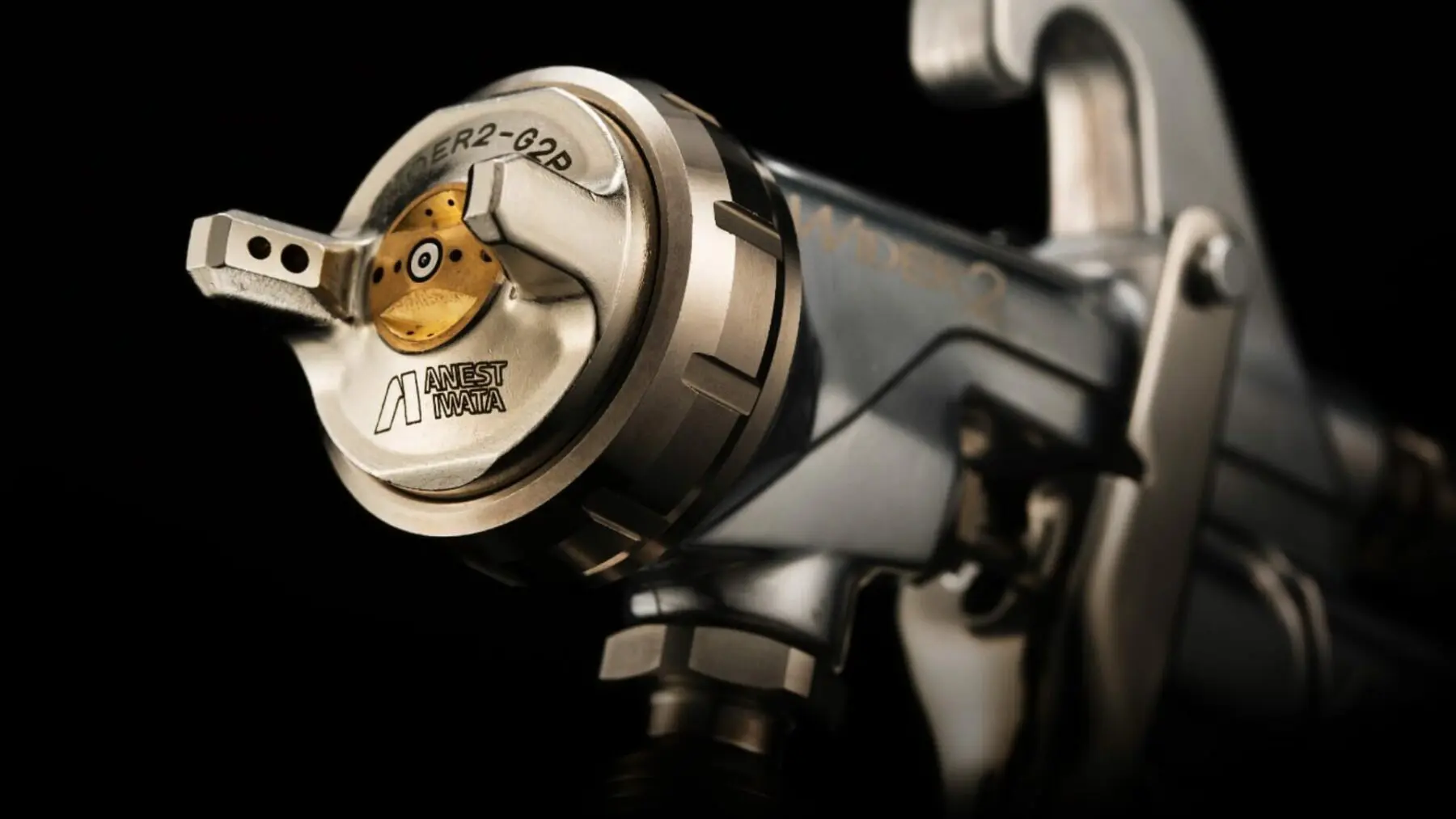
Upgrade spray guns
A continuation of the last point, upgrading your sprayguns to a more efficient gun can make a big difference to the quality of finish as well as your paint consumption. A conventional pressure or gravity spray gun has a transfer efficiency of around 35% compared with an HVLP gun at 65% or more. This means that you could easily halve your paint spend just by upgrading your guns!
It’s worth exploring this in more depth and testing other methods of spraying including Pneumatic Airless, AAA (air assisted airless) or Electric Airless sprayers, and well as more advanced systems like Plural Component or Electrostatic (or a combination of all of these!) for the ultimate efficient spraying process.
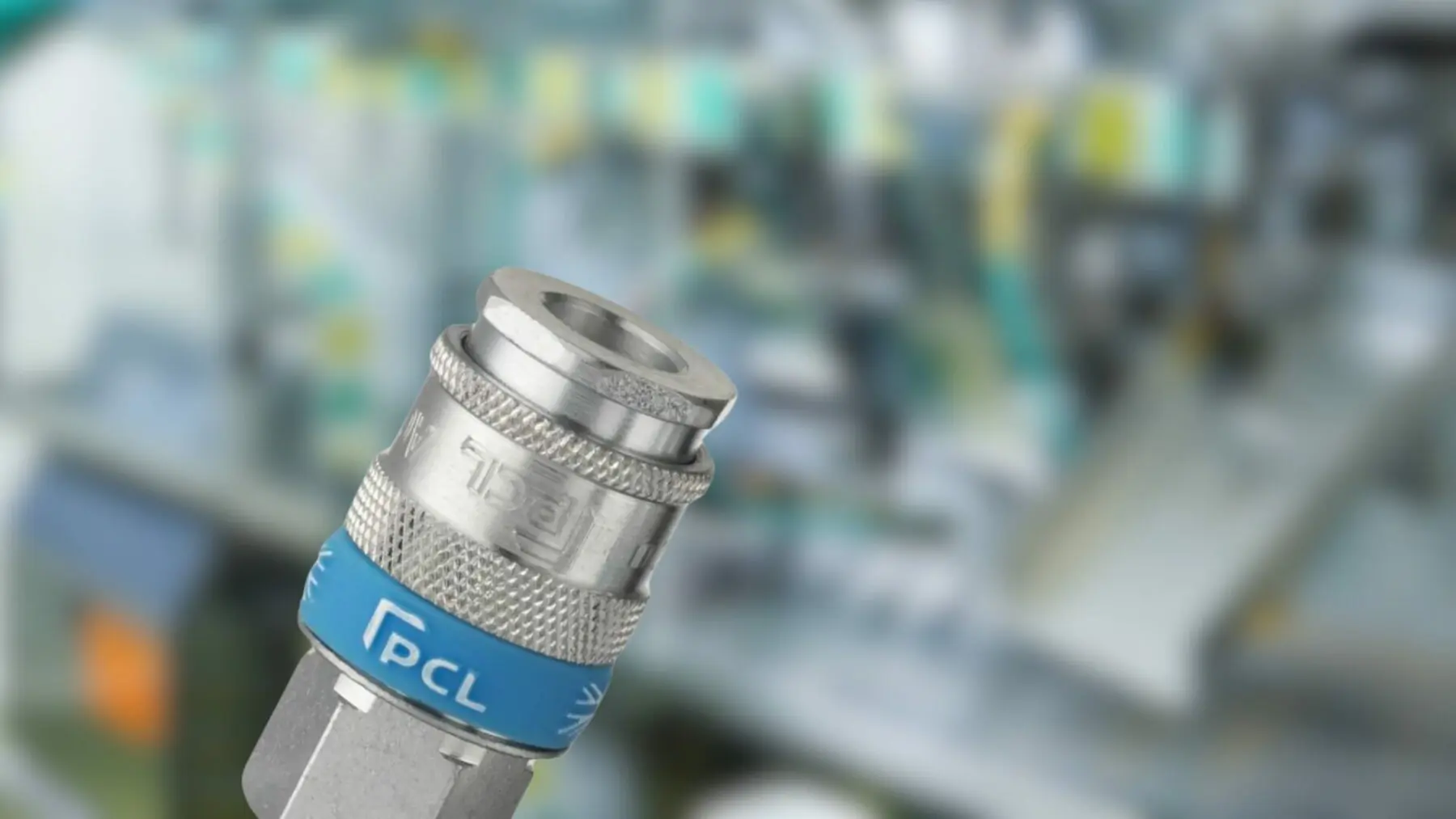
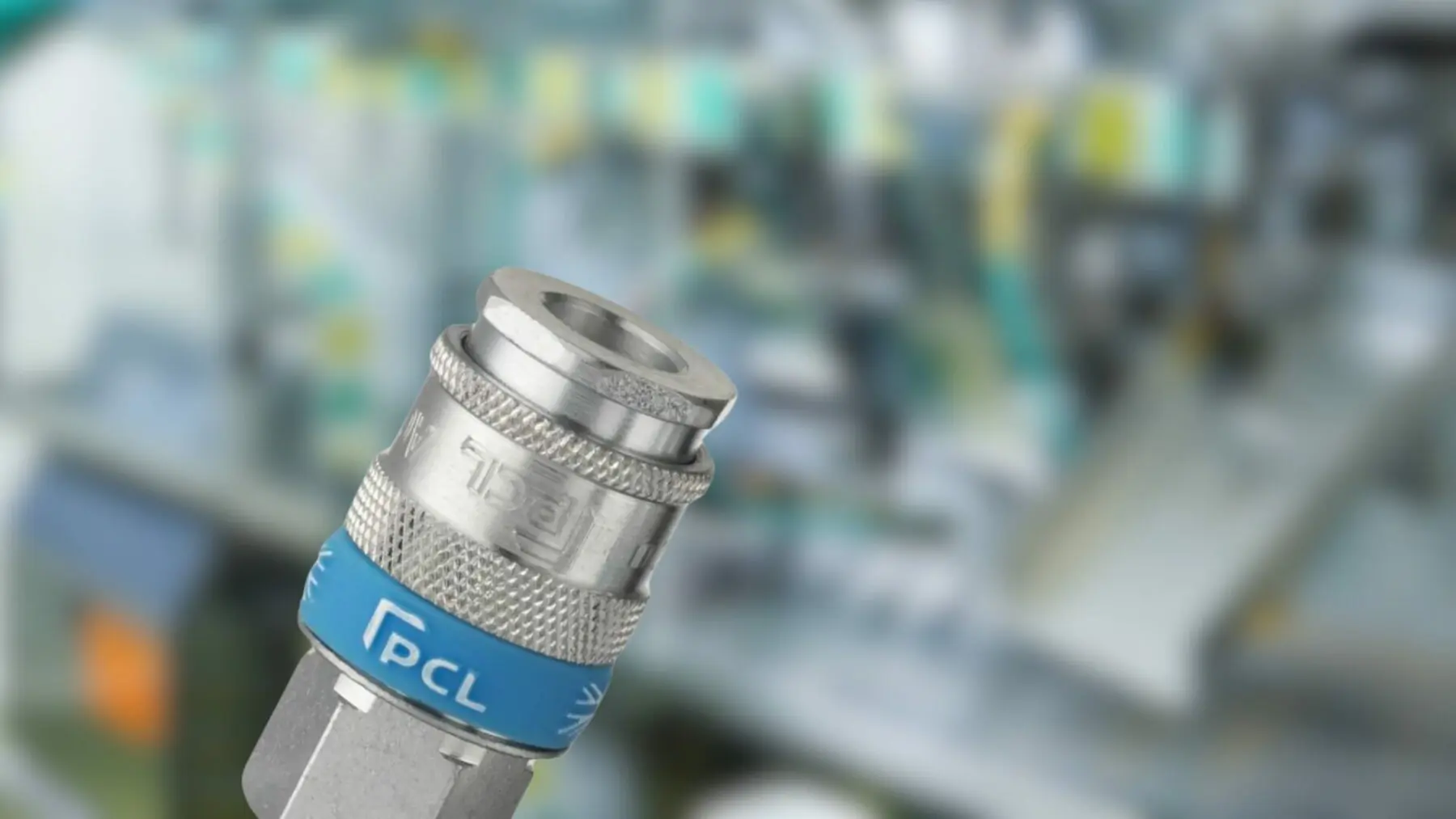
Fit high flow air fittings
By fitting high flow air fittings, you can get up to 70% more airflow than regular fittings. High flow air fittings can be useful for spraying because they can increase the transfer efficiency of the paint quite substantially. HVLP spray guns use a high volume of air at low pressure, which means the sprayed material has less velocity and is less likely to “blow back,” resulting in a softer spray that reduces paint waste and overspray.


Use a spray booth coating
We’ve written a whole article just on this subject as it makes a significant impact on the whole process:
- Dust control: Overspray that’s loosely attached to a spray booth wall can easily detach due to a sprayer brushing against a wall, from the turbulence of the dust extraction, or air from a spray gun. A spray booth coating helps to eliminate dust.
- Better air quality: With cleaner walls comes cleaner air. There will be less contaminants in the air and therefore less rework and defects.
- Increased efficiency: When there are less reworks and defects, throughput is a lot quicker with more time finishing and less time refinishing.
- Enhanced cleanliness: A cleaner work environment encourages operator cleanliness and a more efficient workspace.
- Worker morale: A clean, bright spray booth creates a much better work environment where it is easier to achieve a top-quality finish. This boosts employee morale and efficiency.
There are several solutions that can be used, from tacky surface booth coatings to 5-layer peelable booth coatings, and all have their pros and cons. A multi-layer wall or floor coating is currently the most advanced and efficient solution.
Multi-layer wall coatings like BAXT WP10 are made up of several layers of protective films laminated together. They’re applied in a single application (like a wallpaper) and when the top surface is contaminated, it’s simply peeled off revealing the clean surface underneath. Ideally applied to brand new spray booths before use.
It’s available in a number of versions, including white, clear and other versions for floors, walkways and glue rooms as well.
Pros of Multi-layer Wall Coating
- The ultimate in booth protection
- Very easy to refresh the entire spray booth
- Consistent cleanliness
- Minimal downtime when removing layers
Cons of Multi-layer Wall Coating
- Higher upfront cost
- Required careful application
- Must be applied to new or clean surfaces
Read the full article to see what works best for you.


Upgrade lighting
Often overlooked but vital for quality and efficiency is good quality spray booth lighting. Many booths have old lights that have dimmed over time and the light covers are often covered in overspray. With this happening over many months or years, the difference is often only noticed once you’ve upgraded the lighting.
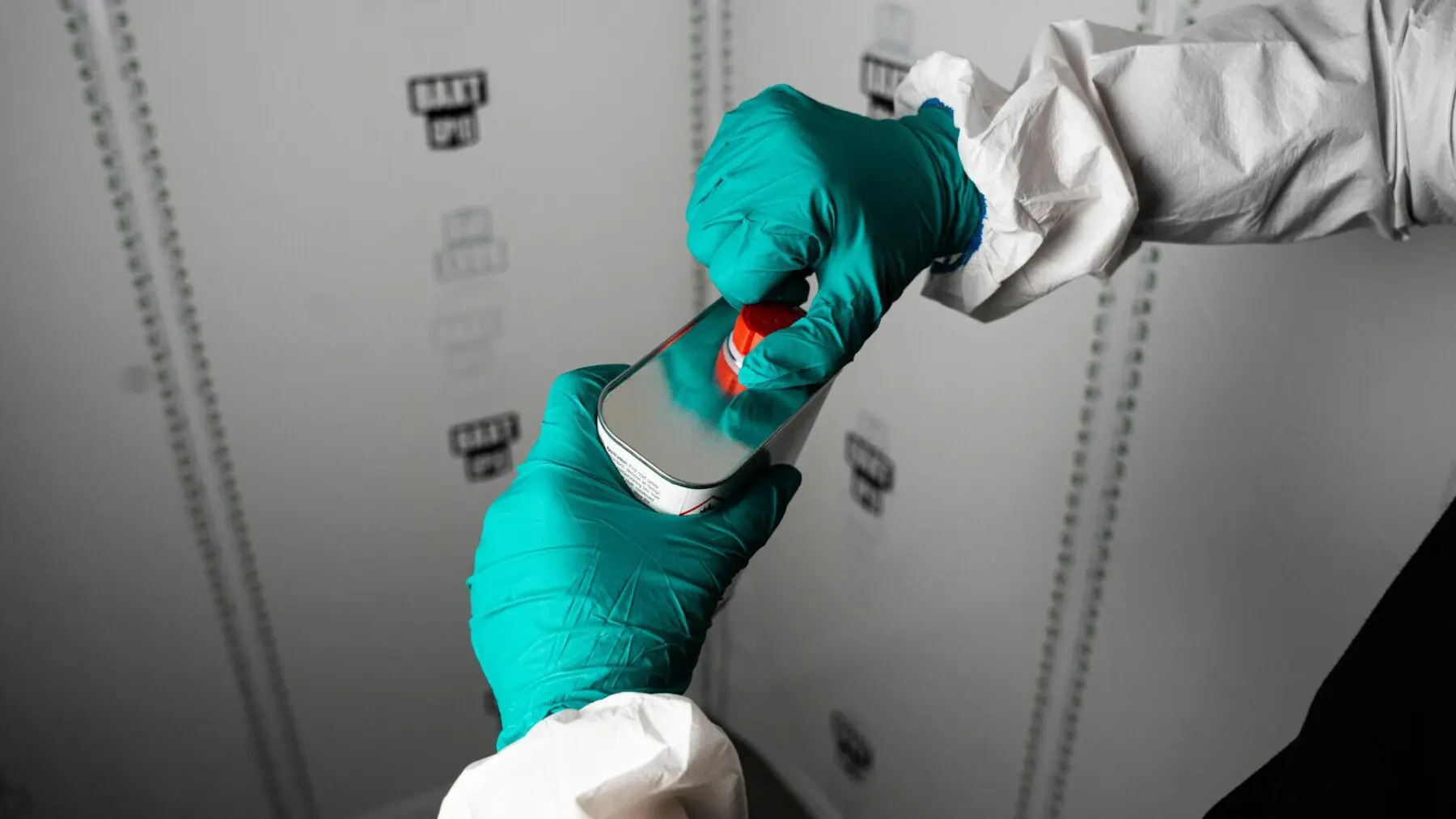
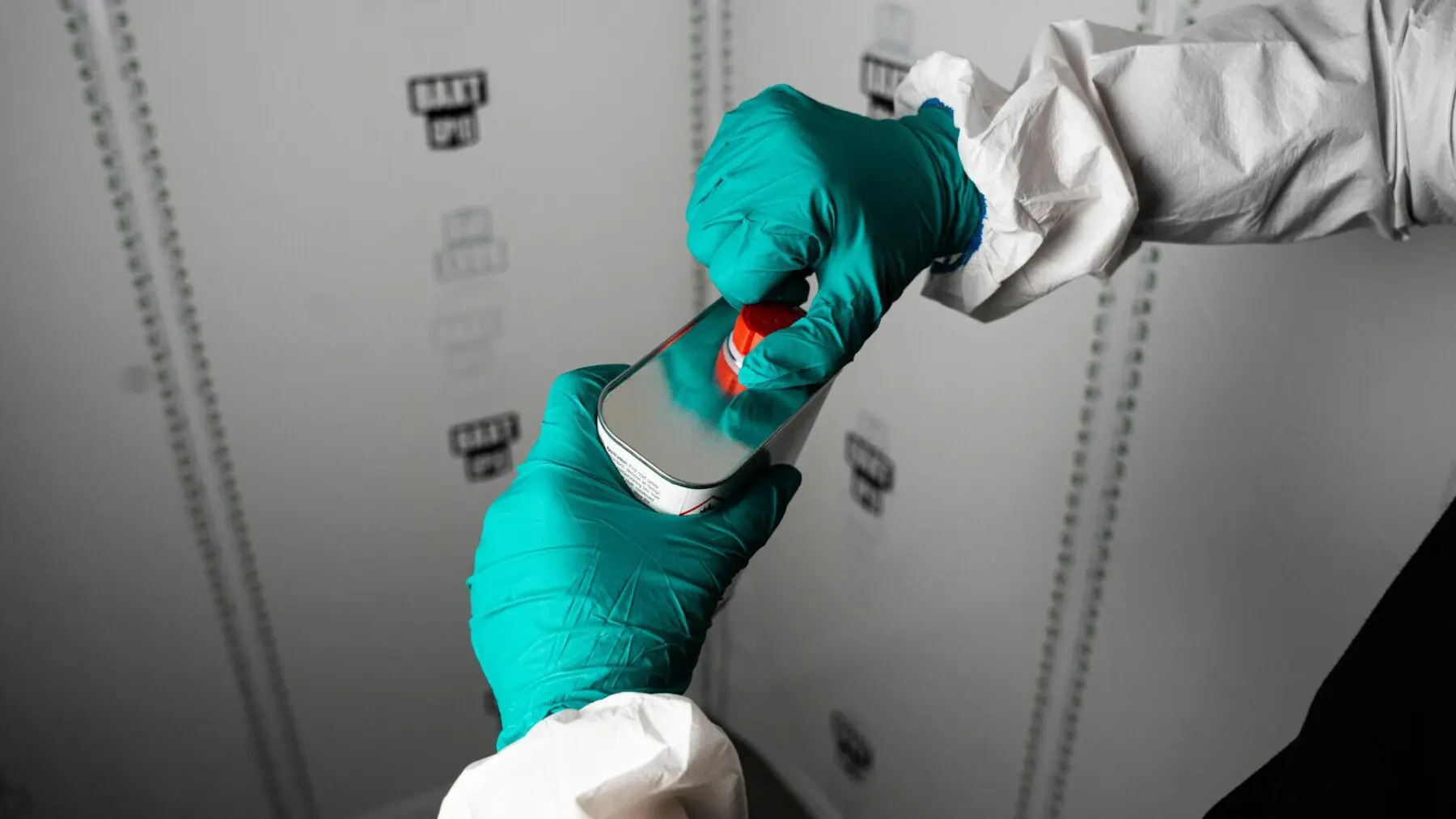
Recycle solvents
Instead of paying to send your used paint and solvents to a solvent recycling company before paying for it again in the form of gunwash, consider a solvent recovery system.
Solvent recyclers remove dirt, debris, and solids from used paint and solvents and distil and recycle the clean solvent which you can use as gunwash. Although there is an initial upfront cost, it can reduce solvent purchases by over 95% and reduce waste disposal costs by over 90%
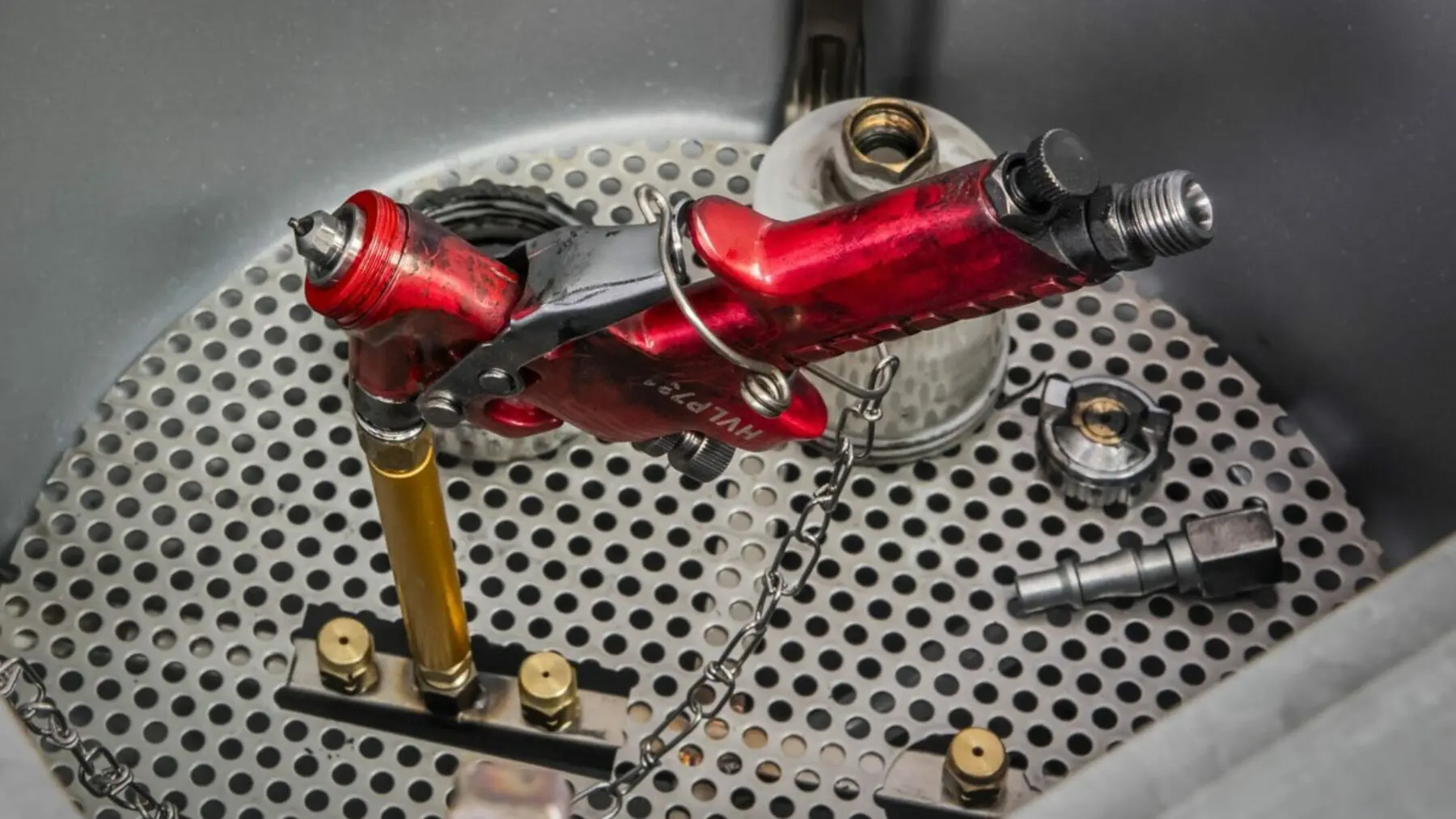
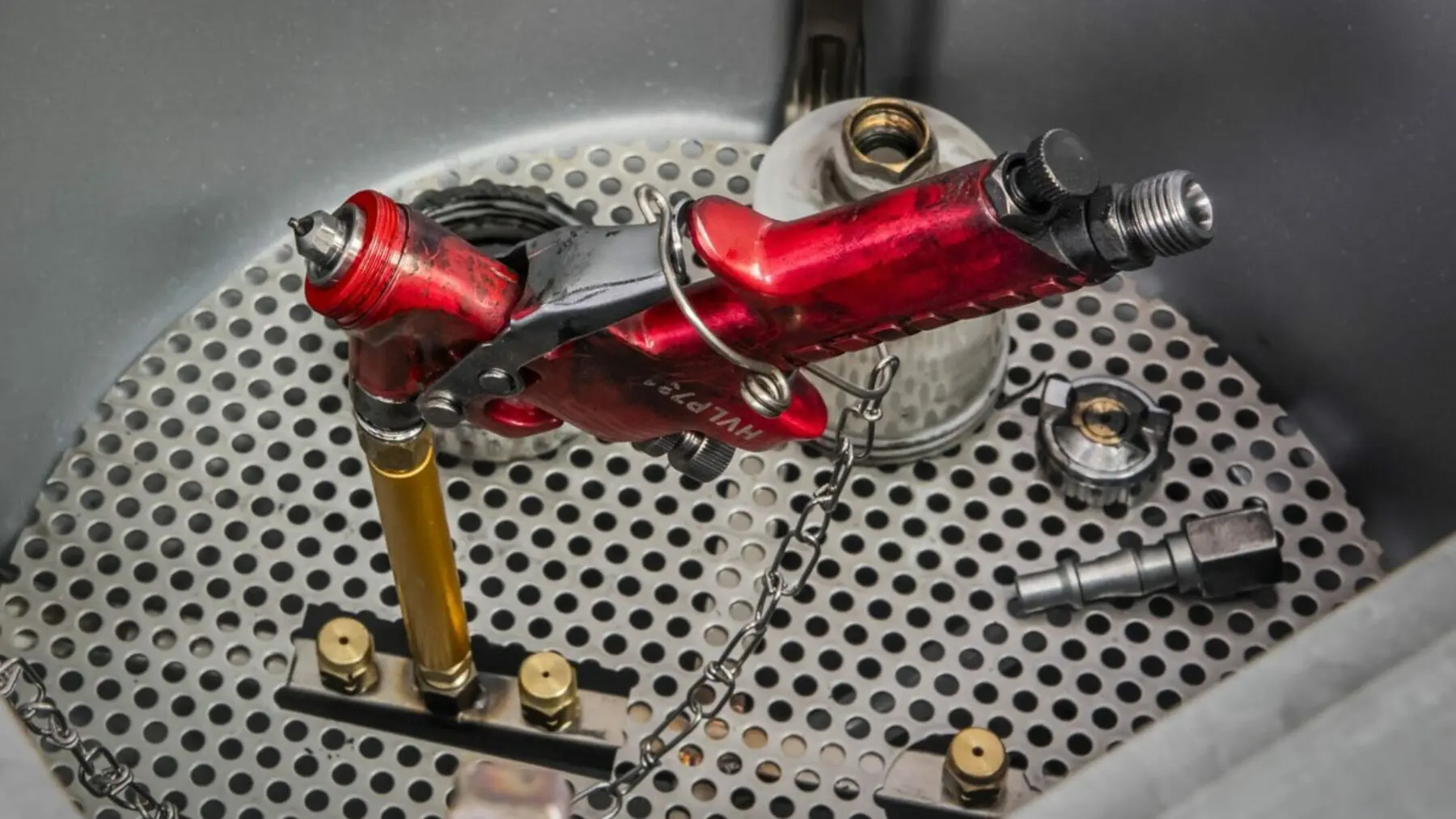
Automatic gun cleaners
Automatic spray gun cleaners save operator time and reduce exposure to solvents but automating the process. Not only is it quicker, safer, and easier, but it saves a lot of money on solvent which gets reused rather than just sprayed into the back of the spraybooth.
The takeaway: find easy wins in improving your paintshop
Although it’s often the last step in your manufacturing process, the painting process has the potential to be the most problematic and costly – particularly if it goes wrong.
Start by picking just one or two easy wins from this list and see the improvements before working through the rest of the items and watch your paintshop become the safe, efficient, and valuable part of the process it should be.
-
Honeywell North Primair PA700 Series ABEK1P3 Powered Air Purifying Respirator (PAPR) Starter Kit£1,162.80 Incl. VAT£969.00 Excl. VAT
-
BAXT WP10 5 Layer Spray Booth Wall Protector£538.80 Incl. VAT£449.00 Excl. VAT
-
BAXT FP10 5 Layer Floor Protection£334.80 Incl. VAT£279.00 Excl. VAT
-
Solvent Recycler 25L Capacity£6,357.60 Incl. VAT£5,298.00 Excl. VAT
-
BAXT C7 Disposable Coverall (PAINTER)£7.14 Incl. VAT£5.95 Excl. VAT
-
BAXT CARBONgrip Premium Nitrile Gloves (50)£11.98 Incl. VAT£9.98 Excl. VAT
-
Solvent Recycler£5,514.00 Incl. VAT£4,595.00 Excl. VAT
-
Portable Mini Spray Gun Cleaner From UnicFrom £952.80 Incl. VATFrom £794.00 Excl. VAT
-
Spraygun Cleaner Automatic – 2 gun, 2 pot cleaner£3,556.80 Incl. VAT£2,964.00 Excl. VAT